- Agglomerated Flux
- welding flux SJ101
- welding flux SJ101G
- welding flux SJ101Q
- welding flux SJ102
- welding flux SJ105
- welding flux SJ201
- welding flux SJ301
- welding flux SJ301A
- welding flux SJ303
- welding flux SJ401
- welding flux SJ501
- welding flux SJ601
- welding flux SJ601B
- welding flux SJ602
- welding flux SJ604
- welding flux SJ605
- welding flux SJ606
- welding flux SJ609
- welding flux SJ609S
- Fused Flux
- welding flux HJ107
- welding flux HJ131
- welding flux HJ230
- welding flux HJ250G
- welding flux HJ257
- welding flux HJ257Z
- welding flux HJ260
- welding flux HJ330
- welding flux HJ350
- welding flux HJ431
- welding flux MD-DZH F600
- SAW Wires
- Welding Wire EL8
- Welding Wire EM12K
- Welding Wire EM13K
- Welding Wire EH14
- Welding wire EA2
- Welding Wire EA4
- Welding Wire H08Mn2SiA
- Gas Shielded Arc Welding Wire
- Welding Electrodes
Add: Zhongling Village, Dayugou Town, Gongyi City, Henan Province, China.
Contact: Mr. Charlie
Tel: +86-371-69596866
Fax: +86-371-64054446
Mobile/Whatsapp/Wechat: +86 18530036598
Skype: charlie.hill700
Postcode: 451271
Email: charlie.ylflux@gmail.com
Agglomerated submerged arc welding flux SJ301A
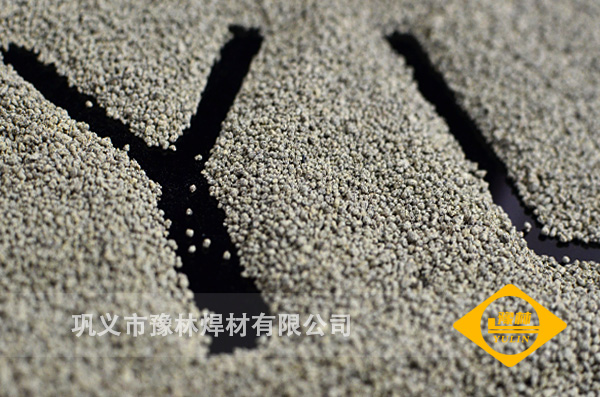
Name: Agglomerated submerged arc welding flux SJ301A
AWS: AWS A5.17/5.23 F6A0-EL12 F7A0-EM12K
SAW wires: EL8, EM12K, etc.
Power supply: DC (DCEP), AC
Basicity: 0.8 BIIW.
Grain size: 10-60 mesh (0.28-2.0mm)
Alloy transfer: Si, Mn alloying
Category: submerged arc welding of mild steel & low-alloy steel
Industry: structural steel, H beams welding, spiral welded steel pipes, pressure vessel, bridge building, ship building, pipeline, boilers, LPG tank, etc.
Description: neutral type calcium-silicate based agglomerated flux. Highly anti-porosity, excellent welding performance, easy slag removal. Maximum energy input could be as high as 1200A. It is featured with short slag, especially suitable for circumferential welding of small diameter pipes. Also applicable for multi-pass welding, double-sided single-pass welding, high speed multiwire welding.
Package: damp-proof packing, 25kg/bag
Certification: ISO
Chemical Composition of Flux (%)
SiO₂+TiO₂ | CaO+MgO | Al₂O₃+MnO | CaF₂ | S | P |
27-37 | 20-30 | 23-33 | 5-15 | ≤0.03 | ≤0.08 |
Mechanical Properties of Deposit Metal
Accompanied Wire | Yield Strength ReH (δs) MPa | Tensile Strength Rm (σb) MPa | Elongation A (δ5) % | Charpy-V lmpact Test (J) | ||
+20℃ | 0℃ | |||||
EL8 | ≥360 | 420-550 | ≥22 | ≥70 | ≥50 | |
EM12K | ≥420 | 500-650 | ≥22 | ≥70 | ≥50 |
Attention:
1. We get values in data sheets from tests carried out in accordance to AWS and GB standard procedure. They only represent values we get under those conditions. They are not to be taken as guarantees. As to welding, individual test results may vary depending on experience & technique, flux type, base metal, joint preparation, flux preparation, ampere, voltage, etc. 2. If welding fluxes are stored in improper environment or influenced by condensed moisture, anyway, they get damp, please dry them at 300-350℃ for 2 hours before usage.
3. Please clean the rust, oil, water on base metal before welding.
4. Add minumum 20% new flux when using recovered flux to avoid welding defects and maintain welding performance & mechanical properties.
5. Please control parameters properly, like preheat temperature, interpass temperature, cooling rate.